- DuPont’s Madison, Wis., manufacturing plant had a need for an additional fermenter in order to increase its capacity for culture production.
- This project was modeled after a plant in Germany and was one of DuPont’s largest installations of its kind in the Midwest. Because Hooper crews worked alongside a continually operating plant, constant communication and understanding of the production process was very important.
- Because the new fermenter had to be craned into the middle of the plant, many existing HVAC, Plumbing, and Fire Protection lines needed to be temporarily relocated. These building utilities were then worked around to incorporate new air handling equipment, a dozen extra back flow preventers, and expanded fire protection coverage.
- Over 4,000 welds were installed on process and support piping systems. They were installed to BPE standards and all production welds were independently videoscoped for review.
- Crews worked in shifts in preparation for the outage which required work around the clock to accomplish the numerous tie-ins with a minimal amount of processing downtime.
- With temporary walls isolating the process areas, there was little room for laydown. Constant parts management from temporary storage trailers and a nearby warehouse kept the crews installing just in time.
https://www.hoopercorp.com/wp-content/uploads/2015/12/IMAG1471.jpg
1080
1910
webadmin
https://www.hoopercorp.com/wp-content/uploads/2021/10/Hooper-logo-copy.png
webadmin2015-12-23 11:27:552016-03-18 15:48:02DuPont
Q28 Van Loon Bottom Rebuild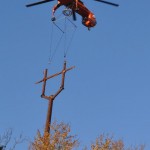
Haymarket Landing
Scroll to top